Recent Posts
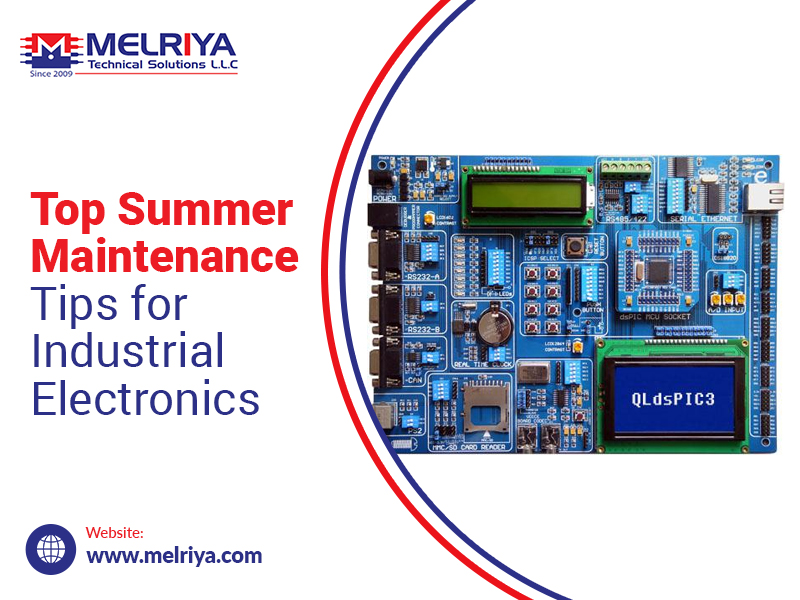
Address
Dubai, U.A.E.Why does the performance of almost every industrial piece of equipment drop when summer temperatures rise? A critical piece of equipment that succumbs to the battering heat is the programmable logic controller (PLC). Actually, these are quite tiny devices, but they run the whole automation system for a lot of things. But in summers, in absence of consideration, many challenges can lead to unexpected PLC failures. The key factor in keeping operations running and needing to avert costly down-time is to know the reasons behind such failures and what preventive measures can be implemented.
Overheating is one of the most identified reasons for PLC failure in summer. While high temperatures tend to stress the internal components of PLC, that stress becomes greater with poor ventilation. In summers, failure or diminished effectiveness of cooling systems in industrial spaces can escalate the temperature of PLCs very quickly, triggering an immediate malfunction in circuit boards. Regular cleaning of air filters, ensuring proper ventilation, or setting up supplementary cooling means such as fans or air-conditioning nearby sensitive equipment comes in handy in such cases.
One other major cause is humidity. Summer humidity spikes condensation which settles therein. Water may corrode metal parts, short-circuit electronic components, and significantly reduce the service life of the equipment. Protection from moisture can be effectively achieved by using an enclosure for PLCs, dehumidifiers, and climate control in the room. Regular inspection for signs of corrosion or moisture damage can detect problems early to avoid becoming worse.
With a lot of power surges and fluctuations, summer is really a very bad season for any PLC. Heavy load from air conditioning and other heavy machinery can cause the power grid to hold up and hence create havoc with the electrical supply. Any sudden voltage rise or drop proved problematic for an array of sensitive electronics within a PLC. Surge protectors and voltage regulators will act to shield the systems from such unpredictable changes and allow them one smooth operational season.
Dust tends to accumulate the more during summer because of a multitude of industries. Such dry and hot conditions create the condition for much dust being thrown up into the air, and from there into the PLCs. Dust will block cooling fans, obstruct ventilation, and insulate the circuit boards, giving rise to egging in further overheating. Periodic cleaning and PL seal applications may work wonders in keeping dust away while ensuring optimal performance.
Another challenge during summer is wiring. Heat and humidity alone will serve to downgrade the insulation of wires faster. Such degradation might lead to short circuits or signal loss, which, in turn, will stop the PLC from executing its function. Regularly scheduled maintenance checks on all wiring, connections, and terminals are important. These checks should include looking for signs of wear, and replacement of all components found to be compromised should occur before bigger problems arise.
Preventive maintenance remains the best form of defense against damage. Thorough inspections of PLCs in the months before summer would go a long way in ensuring that cooling systems are running, enclosures are intact, batteries are well charged and wiring is secure. Maintenance activities have also to be documented for trend tracking and possibility of spotting recurring problems that would eventually lead to more effective preventive strategies over time.
Training in recognizing early signs of distress in PLCs such as uncalled resets, slow responses or error messages could even help cars get to them faster for intervention. The sooner problems are detected, the easier and cheaper they are to fix. Organizing refresher training programs at the beginning of summers can make sure few employees would sit back and watch when it comes to those critical months.
Summer really brings real and serious threats to PLC systems; however, this many risks could be mitigated through careful preparation. Overheating, humidity, power fluctuations, dirt, wiring degradation, and human error all contribute to seasonal failures, but proper planning, timely maintenance, and environmental control would keep the systems running reliably. Melriya Technical Solutions L.L.C cares about helping you maintain protection on all of your automation assets, whatever the season. Proactive measures today can save time, dollars, and frustration tomorrow.